Wellenausrichten per Laser - Unsere Passion und Ihre Präzision
Wir kümmern uns um Ihre Anlage - Zustandsorientierte Instandhaltung ist unsere Expertise

PRÜFTECHNIK, der Erfinder des laseroptischen Wellenausrichtens, verfügt über 30 Jahre Erfahrung in der Entwicklung, Herstellung und Anwendung laseroptischer Ausrichtsysteme. Wir bieten eine breite Palette an Wellenausrichtsystemen.
Unsere modularen Systeme können individuell ausgestattet und in ihren Funktionen erweitert werden. Die Systeme sind auch als ATEX/EX-Versionen für die Nutzung in explosionsgefährdeten Bereichen erhältlich. Unsere Messsysteme werden weltweit in den verschiedensten Anwendungen zur Ausrichtung rotierender Maschinen in den meisten Industrien eingesetzt

Präzise Maschinenausrichtung zahlt sich aus
Fehlausrichtung vermeiden
Rotierende Maschinen sind anfällig bei Fehlausrichtungen. Wird eine neue Maschine bereits bei der Inbetriebnahme korrekt ausgerichtet und später regelmäßig kontrolliert, können in erheblichem Umfang Betriebs- und Instandhaltungskosten gespart werden.
Lasergenaues Ausrichten erhöht die Nutzbarkeit von Maschinen, weil deren Ausfallrate sinkt. Zudem schützt es die Anlage und steigert die Produktqualität, da die Schwingung auf das geringstmögliche Maß reduziert wird.
Bei einer Fehlausrichtung erhöht sich die Last auf die Kupplung extrem, da Reaktionskräfte in der Kupplung erzeugt werden.
Die Vorteile des Wellenausrichtens
Geringerer Stromverbrauch

Durch genaues Ausrichten kann erheblich Strom eingespart werden. Lasergenaues Ausrichten schließt Reaktionskräfte aus und kann den Energieverbrauch um bis zu 10 % reduzieren.
Weniger Reparaturen

Mechanische Dichtungsreparaturen nehmen um bis zu 65% ab, wenn regelmäßig präzise ausgerichtet wird.
Der Reparaturanteil an den Wartungskosten nimmt spürbar um bis zu 30 % ab, wenn lasergenaues Wellenausrichten integraler Bestandteil des Pumpenwartungsprogramms ist
Lasergenaues Ausrichten führt zu Einsparungen bei den Wartungsausgaben, da die Ersatzteil- und Lagerkosten sinken
Längere Lebensdauer

Je größer der Versatz, desto geringer ist die mechanische Lebensdauer der Lager
Traditionelle Wellenausrichtmethoden
Konventionelle Methoden wie Haarlineal oder Fühlerlehre
hängen von der begrenzten Auflösung des menschlichen
Auges und den Kupplungsoberflächen ab. Die erreichbare Auflösung von 0,1 mm ist für die meisten Maschinen viel zu gering.
Durchhang der Messuhrenhalterungen
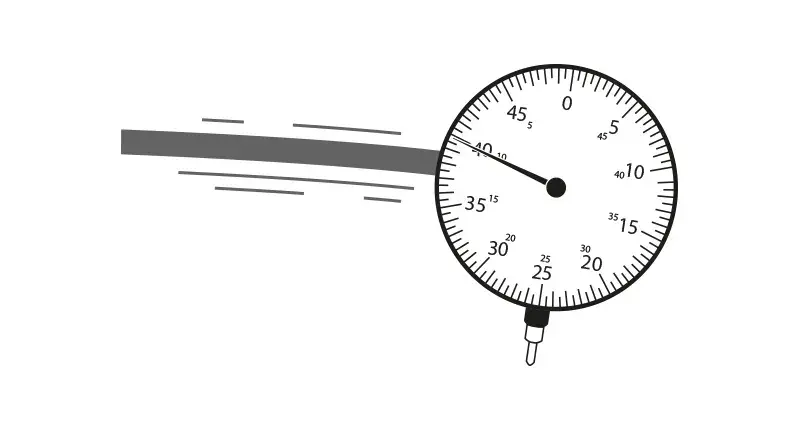
Der Messstangendurchhang sollte immer vor der eigentlichen Ausrichtmessung bestimmt werden, egal wie stabil die Halterungen erscheinen mögen.
Geringe Auflösung

Bei jeder Ablesung kann beim Runden ein Fehler von bis zu 0,005 mm entstehen. Während einer Gesamtmessung können sich diese Fehler auf einen Wert von bis zu 0,04 mm summieren.
Innere Reibung/Hysterese

Gelegentlich muss leicht gegen die Messuhr geklopft werden, damit der Zeiger die endgültige Position einnimmt.
Obwohl Messuhren eine Auflösung von 0,01 mm erzielen, sind die Berechnungen meistens kompliziert und unterliegen vielen Einflussfaktoren, die die Genauigkeit reduzieren. Diese Methoden sind anfällig für menschliche Fehler beim Ablesen der Anzeigewerte oder der Berechnung des Ausrichtzustands.
Spiel in den mechanischen Verbindungen

Geringes Spiel, das möglicherweise gar nicht wahrnehmbar ist, kann bereits zu erheblichen Messfehlern führen.
Ablesefehler

Fehler können leicht auftreten, wenn die Anzeigen unter Zeitdruck und bei schlechten Bedingungen abgelesen werden müssen.
Schief angebrachte Messuhr
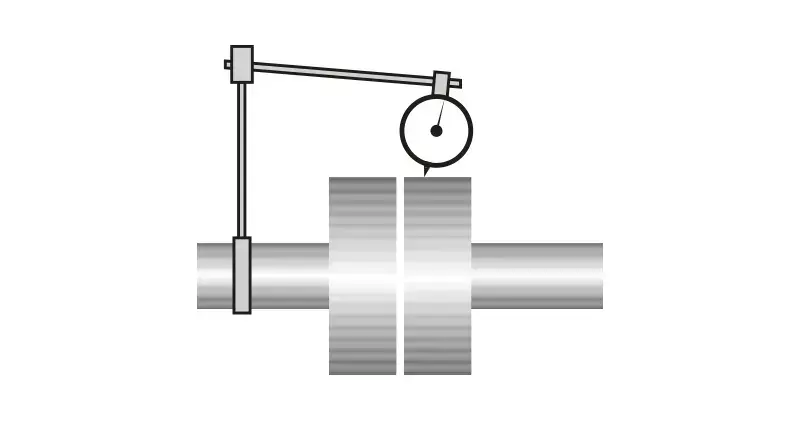
Ist die Messuhr nicht senkrecht zur Messfläche angebracht, wird tendenziell ein zu großer Messwert erfasst.
Axiales Wellenspiel

Axiales Wellenspiel kann die Klaffungsmesswerte am Flansch, die zur Messung des Winkelversatzes aufgenommen werden, verfälschen - es sei denn, es werden zwei axial montierte Messuhren verwendet.